Para entrar en contexto, imagine una fábrica que no sólo sabe cuándo algo está a punto de fallar sino, que, en teoría, podría llegar hasta a rediseñar sus propias piezas, adaptarse al entorno y aprender de cada ciclo productivo (lo sé, suena bastante complejo pero, la idea es ir desarrollado el tema para que sea más claro). Ya no hablamos de un concepto futurista, sino de una realidad cercana: las Industrias 4.0 ha alcanzado un nuevo umbral, donde las máquinas son parte de sistemas inteligentes que aprenden, se optimizan y actúan por sí mismos.
Mantenimiento predictivo
Durante décadas, el mantenimiento fue una labor reactiva: algo se dañaba y se reparaba. Ahora, la idea es que con sensores distribuidos (IoT), algoritmos de inteligencia artificial y la inteligencia humana en el proceso, los equipos industriales pueden anticipar fallos días o semanas antes de que ocurran. Vibraciones anómalas, cambios de temperatura o variaciones de flujo eléctrico se convierten en señales tempranas que permiten tomar decisiones antes de que el daño sea real.
Este enfoque ha demostrado resultados contundentes: reducciones de hasta el 50% en el tiempo ocioso o de inactividad y ahorros de hasta el 20% en mantenimiento, según estudios de McKinsey.
Diseño generativo
El diseño generativo puede llevar el concepto de innovación al siguiente nivel. En lugar de esbozar soluciones, los ingenieros establecen objetivos y restricciones —peso, resistencia, material— y permiten que una IA explore muchas de las variantes posibles en pocas horas. El resultado en su mayoría de las veces son formas y estructuras que parecen más naturales que artificiales, inspiradas muchas veces en patrones biológicos.
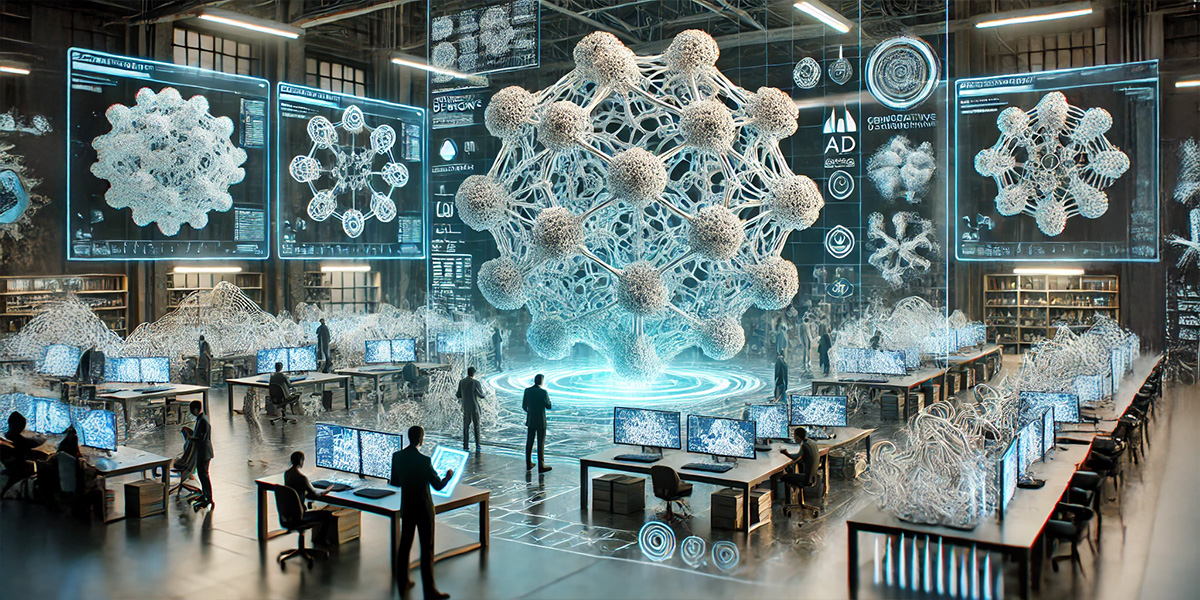
La Sinergia
Lo más transformador no está en cada tecnología por separado, sino en su integración. Cuando el mantenimiento predictivo se convierte en retroalimentación para el diseño generativo, se establece un ciclo de mejora continua y autónoma. Las máquinas no sólo previenen fallos, sino que diseñan mejores versiones de sí mismas basadas en datos reales. Esta convergencia habilita:
- Personalización masiva sin aumento excesivo de costos, desde prótesis personalizadas hasta turbinas adaptadas a condiciones específicas.
- Sostenibilidad, al reducir desperdicios, consumo energético y fallos inesperados.
- Ciclos productivos regenerativos, donde cada fallo detectado se convierte en una oportunidad de rediseño estructural.
Pero no todo es felicidad, la obsolescencia programada es un riesgo
Pero este nuevo paradigma también trae preguntas incómodas. ¿Qué pasa cuando una fábrica puede rediseñar una pieza defectuosa? ¿Será para mejorar su vida útil… o para ajustarse a un ciclo de consumo forzado que va a mejorar los ingresos del fabricante de los sistemas en lugar de cuidar los presupuestos de los usuarios en la industria?
La obsolescencia programada, ese mecanismo deliberado por el cual muchos productos son diseñados para fallar antes de lo necesario, podría adquirir nuevas formas en la era de las Industrias 4.0. En teoría, tecnologías como el mantenimiento predictivo y el diseño generativo abren la puerta a una fabricación más duradera, resiliente y sostenible. Sin embargo, en la práctica, estas mismas herramientas también podrían servir para perfeccionar estrategias que perpetúan el ciclo del consumo forzado.
Durante décadas, muchos fabricantes han acortado artificialmente la vida útil de dispositivos no porque hayan llegado al fin de su capacidad técnica, sino porque un producto que dura demasiado ya no es un buen negocio. La idea de que un electrodoméstico, un teléfono o una impresora duren diez o quince años sin fallos resulta inconveniente en un modelo económico basado en ventas recurrentes. Con la sofisticación de la inteligencia artificial y el acceso masivo a datos de uso en tiempo real, las empresas ahora podrían programar no solo la fecha estimada de fallas, sino justificar esas fallas como parte de una “actualización necesaria” o una “mejora optimizada”.
Lo que se presenta como innovación puede, en ciertos casos, ocultar una nueva generación de obsolescencia, más difícil de detectar y más fácil de racionalizar. En lugar de cables que se rompen o baterías que se agotan, podríamos enfrentarnos a algoritmos que degradan el rendimiento “por seguridad” o diseños que excluyen la reparación como opción viable. La promesa de eficiencia, si no está acompañada de transparencia y ética, corre el riesgo de seguir alimentando una economía de lo descartable, solo que ahora impulsada por inteligencia artificial.

El desafío ético
Lejos de reemplazar al ser humano, esta evolución tecnológica redefine su rol. Las fábricas del futuro no estarán vacías, pero sí serán más inteligentes. Los trabajadores ya no serán operarios de máquinas, sino estrategas de datos y decisiones complejas, responsables de interpretar información y dirigir procesos de mejora continua. Ya existen robots que ajustan su producción en tiempo real, cadenas de suministro que se anticipan a interrupciones geopolíticas o climáticas, y líneas de ensamblaje que reconfiguran su orden en función del inventario y la demanda. Es como si la fábrica fuera una especie de organismo autoorganizado, adaptativo y resiliente.
La supervivencia de las Industrias 4.0
Las Industrias 4.0, en su etapa madura, ya no son una opción estratégica, sino una condición para la permanencia y relevancia de los negocios en un entorno cada vez más competitivo. Sin embargo, la adopción exige algo más que eficiencia: requiere un compromiso ético real. Porque no se trata solo de producir más o más rápido, sino de crear con propósito, de usar la inteligencia artificial no para fomentar el consumo innecesario, sino para resolver necesidades auténticas, reducir desperdicios y construir un futuro productivo más justo, sostenible e inclusivo.